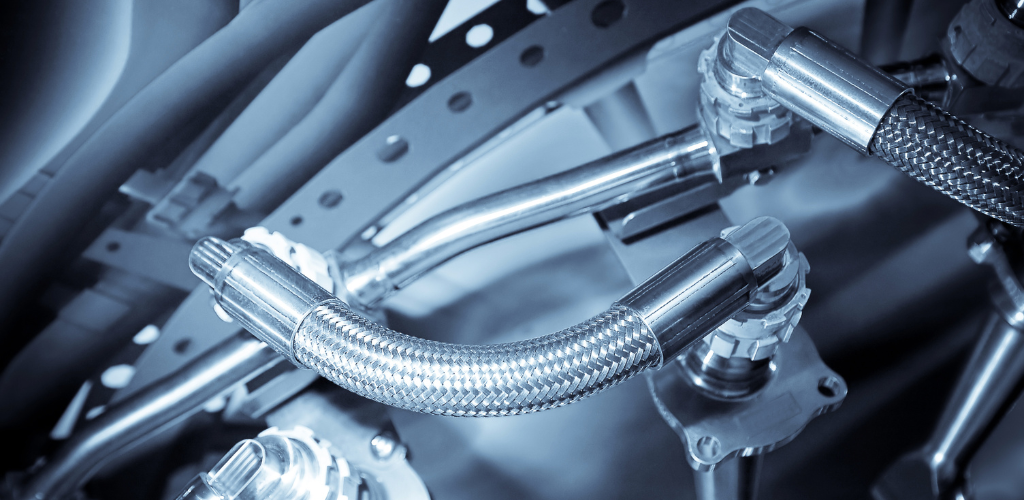
Case Study - producent zaawansowanych systemów hydrauliki siłowej
Analiza Stanu Obecnego jako podstawa transformacji procesowej
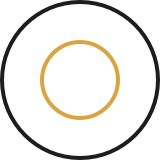
Analiza finansowa:
- Analiza przychodów i kosztów do poziomu zysku ze sprzedaży
- Wariant porównawczy P & L (uwzględniony przyrost zapasów oraz produkcja na potrzeby własne)
Planowanie i organizacja produkcji:
- Analiza efektywności wykorzystania parku maszynowego
- Badanie metod i standardów organizacji pracy
- Ocena efektywności wykorzystania zasobów ludzkich
- Ocena poziomu dostępności produktów
- Analiza poziomu zapasów
Zakupy produkcyjne:
- Analiza alternatywnych dostawców pod kątem redukcji cen materiałów produkcyjnych
Sprzedaż / procesy wspierające:
- Ocena efektywności wykorzystania zasobów ludzkich
- Badanie metod i standardów organizacji pracy
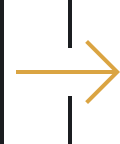
Standardowy proces analizy stanu obecnego składa się z trzech głównych etapów, które pozwalają na pełne zrozumienie organizacji i jej wyzwań:
ETAP 1: Przygotowanie prac
- Spotkanie z głównymi interesariuszami – identyfikacja ryzyk.
- Komunikacja działań do całej organizacji.
- Opracowanie harmonogramu prac projektowych.
🕒 Czas trwania: 1 tydzień
ETAP 2: Analiza stanu obecnego
- Identyfikacja realizowanych procesów.
- Mapowanie procesów biznesowych.
- Analiza efektywności wykorzystania zasobów ludzkich oraz parku maszynowego.
- Określenie potencjału do wzrostu zdolności produkcyjnych.
🕒 Czas trwania: 2-3 tygodnie
ETAP 3: Opracowanie rekomendacji zmian
- Zaprojektowanie stanu docelowego dla analizowanych procesów.
- Opracowanie Road Mapy prac wdrożeniowych.
- Określenie efektów biznesowych dla wypracowanych rozwiązań wraz z wpływem na P&L.
🕒 Czas trwania: 1-2 tygodnie
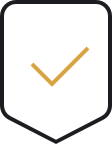
Kluczowe rezultaty po wprowadzeniu rekomendacji po przeprowadzonej Analizie Stanu Obecnego obejmowały oszczędności w następujących obszarach:
- zakupy produkcyjne – 2,85 mln zł
- koszty kooperacji – 700 tys. zł
- koszty pracy – 3 mln zł
- poziom zapasów półproduktów i WIP – 1,4 mln zł
A dodatkowo:
Optymalizacja procedur oraz wprowadzenie standardów pracy pozwoliły znacząco zmniejszyć czas nieproduktywny związany z przestojami maszyn.
Lepsza synchronizacja zakupów z produkcją pozwoliły ograniczyć nadmierne magazynowanie surowców i półproduktów.
Dzięki wdrożeniu standardów operacyjnych i poprawie organizacji pracy procesy stały się bardziej płynne, a wykorzystanie zasobów – bardziej efektywne.
Dzięki lepszemu planowaniu i eliminacji wąskich gardeł firma była w stanie realizować zamówienia zgodnie z harmonogramem, co przełożyło się na lepsze relacje z klientami.
Jednym z najważniejszych efektów była zmiana podejścia pracowników do pracy. Wspólne wypracowanie standardów i aktywne angażowanie zespołu w proces zmian sprawiło, że ludzie poczuli się częścią transformacji, a nie tylko jej biernymi odbiorcami.
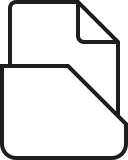
Opis firmy klienta
Firma produkcyjna z wieloletnim doświadczeniem, specjalizująca się w projektowaniu i produkcji zaawansowanych systemów hydrauliki siłowej. Obsługuje szerokie spektrum branż przemysłowych, dostarczając komponenty o wysokiej precyzji i niezawodności. Posiada rozbudowaną infrastrukturę produkcyjną i, aby sprostać rosnącym wymaganiom rynku, stale inwestuje w rozwój technologiczny.
Kluczowe informacje o firmie:
- Branża: Produkcja
- Główne obszary działalności: Produkcja wyrobów przemysłowych, w tym obróbka, montaż oraz zarządzanie sterowaniem produkcją.
- Struktura organizacyjna:
- Działy obejmują m.in. produkcję, logistykę, zakupy, sprzedaż, marketing, finanse, kadry, obsługę klienta, badania i rozwój oraz jakość.
- Zatrudnienie: Na moment analizy firma zatrudniała około 400 osób, z czego największy udział miał dział produkcji (ok. 70% pracowników).
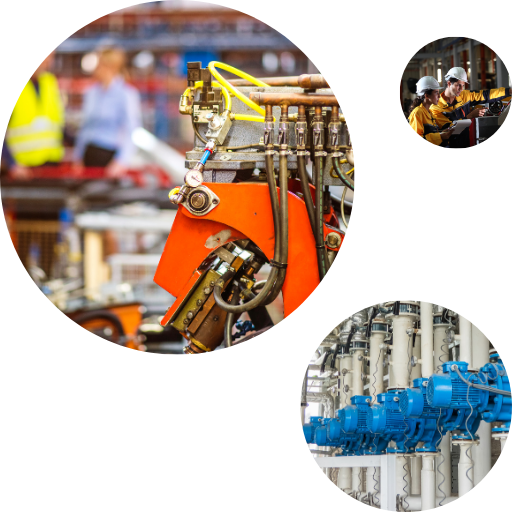
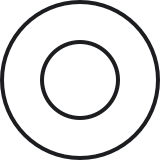
Kluczowe wyzwania na podstawie Analizy Stanu Obecnego
Brak zarządzania efektywnością pracy – szczególnie w obszarach administracyjnych, gdzie występuje wysoki poziom czynności niedodających wartości (NVA). Wskaźniki NVA w niektórych działach osiągały nawet 59%, co wpływało na spadek efektywności i produktywności.
Brak standaryzacji metod i organizacji miejsca pracy – w firmie zauważono niski poziom standaryzacji działań, co prowadziło do nieefektywności operacyjnej, problemów z ergonomią pracy oraz wysokiego poziomu marnotrawstwa powierzchni i zasobów ludzkich.
Nieefektywność procesów produkcyjnych – niska utylizacja parku maszynowego, brak analizy czasów przestojów i ograniczona kontrola nad efektywnością pracy operatorów.
Problemy z realizacją zamówień – wskaźnik OTIF na poziomie 74%.
Wysoki poziom zapasów – nadmierne zamrażanie kapitału i ograniczenie płynności finansowej firmy.
Problemy z organizacją planowania produkcji – brak narzędzi do skutecznego planowania oraz brak systemu wskaźników monitorujących realizację planów produkcyjnych.
Słabe zarządzanie zespołem i brak jasno określonych standardów pracy menedżerów – brak jasno określonych ról i oczekiwań względem liderów.
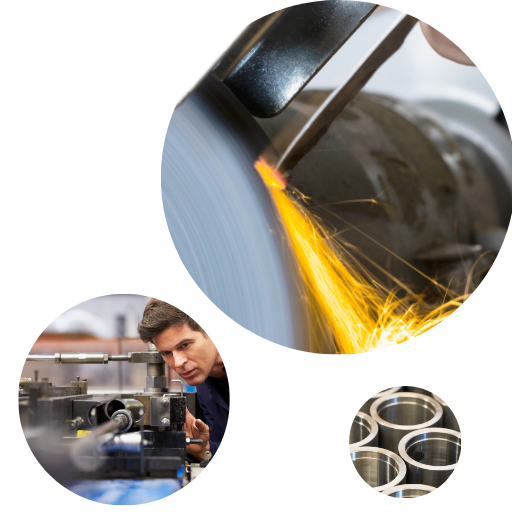
REKOMENDACJE DLA OBSZARU PRODUKCJI
- Organizacja ergonomicznych stanowisk pracy zapewniających większą efektywność pracy.
- Nowe podejście do normowania czasów operacji/procesów oraz weryfikacja aktualnie przyjętych norm.
- Opracowanie wizualnych standardów pracy dla poszczególnych stanowisk produkcyjnych.
- Uruchomienie programu kształcenia operatorów w zakresie standardów pracy z wykorzystaniem techniki TWI.
- Uruchomienie systemu wskaźników oraz ich raportowania w celu zarządzania efektywnością pracy na produkcji.
- Rozwój kompetencji pracowników produkcyjnych w celu zapewnienia elastyczności funkcjonowania obszarów układania i montażu.
- Wdrożenie systemu zarządzania wynikami pracy – wskaźniki operacyjne zapewniające realizację celów strategicznych.
- Implementacja Zarządzania Wizualnego.
- Uruchomienie cyklicznych spotkań typu Boardmeeting, mających na celu realizację cyklu CEL-WYNIK-PROBLEM-KAIZEN.
- Wdrożenie autonomicznych zespołów – wzmocnienie pracy zespołowej i kultury delegowania uprawnień na coraz niższych szczeblach organizacji oraz wypracowanie nowego standardu komunikacji.
REKOMENDACJE DLA OBSZARU ŁAŃCUCHA DOSTAW
- Zaprojektowanie i uruchomienie procesu strategicznego planowania – S&OP, kroczące planowanie średnio i długo terminowe.
- Wdrożenie cykli spotkań procesu S&OP – zbudowanie świadomości i podejścia do rozwiązywania problemów w oparciu o fakty (KPI).
- Dostosowanie danych w tablicach planistycznych do realnych wydajności produkcyjnych (aktualizacja cykliczna weryfikacja norm).
- Określenie Re-order point i Safety Stock dla produktów, komponentów i materiałów.
- Wdrożenie planowania opartego o strategie wytwarzania postponement dla produktów o wspólnym „półprodukcie”.
- Wdrożenie narzędzi prognozowania sprzedaży zawierających narzędzia statystyczne i ekonometryczne – monitorowanie sprzedaży towarów handlowych.
- Wdrożenie wskaźników Łańcucha Dostaw.
- Wdrożenie mechanizmu monitorującego postęp wykonania harmonogramu produkcji (zarządzanie wizualne).
- Uruchomienie cyklicznych odpraw Łańcucha Dostaw – spotkanie w środowisku kross funkcjonalnym mające na celu w sposób ustrukturyzowany przekazywanie informacji i rozwiązywanie problemów o dziennych odchyleniach i występujących ryzykach nie realizacji zamówień.
- Usprawnienie procesu przyjęcia na magazyn oraz stworzenie systemu zapewniającego aktualizacje danych podstawowych dla systemu Kanban
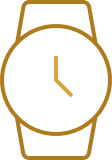
Analiza Stanu Obecnego trwała 10 tygodni i obejmowała szczegółową ocenę procesów produkcyjnych, organizacji pracy oraz wykorzystania zasobów.
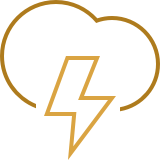
- Dział Finansowy – odpowiedzialny za analizę kosztów, rentowności oraz efektywności finansowej.
- Dział Produkcji – kluczowy obszar badania, obejmujący analizę efektywności wykorzystania parku maszynowego, metod organizacji pracy oraz problemów związanych z postojami.
- Dział Sprzedaży – uczestniczył w analizie procesów sprzedażowych oraz w opracowaniu rekomendacji dotyczących optymalizacji procesów handlowych.
- Dział Logistyki i Zakupów – odpowiedzialny za analizę łańcucha dostaw, dostępności materiałów oraz optymalizacji procesów zakupowych.
- Dział HR – angażował się w analizę efektywności wykorzystania zasobów ludzkich, struktury organizacyjnej oraz wyzwań związanych z zarządzaniem personelem.
- Dział Jakości – analizował procedury kontroli jakości, standardy produkcyjne oraz poziom zgodności produktów z wymaganiami.
- Dział Technologiczny – badał aspekty związane z procesami produkcyjnymi, wdrażaniem nowych technologii oraz optymalizacją pracy maszyn i operatorów.
- Dział Obsługi Klienta i Eksportu – oceniał skuteczność procesów obsługi klienta, poziom satysfakcji oraz potencjalne obszary do usprawnień.
Jeśli Twoja organizacja zmaga się z podobnymi wyzwaniami, warto rozważyć przeprowadzenie rzetelnej Analizy Stanu Obecnego. To pierwszy krok do lepszej przyszłości! Porozmawiajmy o najpilniejszych wyzwaniach Twojej firmy. Wypełnij formularz bezpłatnej konsultacji, a my w ciągu 48h skontaktujemy się z Tobą i wspólnie pomożemy Ci dobrać idealne rozwiązanie na miarę potrzeb Twojej firmy.