Ostatnia aktualizacja: 24.02.2023
Nauka Lean to nie jazda windą, lecz chodzenie po schodach. Idąc po schodach, masz szansę przemyśleć swój kolejny krok, uczysz się pokonując każdy stopień. Doceń szczególnie te, w których musisz cofnąć się o krok, przemyśleć, by móc wspinać się znowu. Jadąc windą na pewno nie zrozumiesz co działa, a co nie.
W Artykule:
Czy wiesz, jaki jest ulubiony temat rozmowy mężczyzn? Podobno najlepiej się czują, kiedy w rozmowie jest dużo o nich samych. Egocentryzm to domena płci męskiej – mówi z uśmiechem Radek Drzewiecki, założyciel Leanpassion i pomysłodawca popularnej edukacyjnej platformy streamingowej dla biznesu Youniversity.be. W tym artykule opowiemy historię o tym, w jaki sposób doszło do tego, że Lean stał się jego życiową pasją. Jeśli interesujesz się filozofią Lean, w tym magicznym, świątecznym czasie refleksji zapraszamy do lektury, być może będzie dla Ciebie inspiracją. Magicznych Świąt!
Spis treści:
- Zdrowy rozsądek jako sedno Lean
- Lean to nie szkolenia
- Lean to nie szybsza praca
- Lean to nie zestaw narzędzi
- Dlaczego liderzy nie wierzą w siłę Lean?
- Pozwól mi zrobić, a zrozumiem
Zobacz też: Mity na temat Lean
Zdrowy rozsądek jako sedno Lean
Jakieś 20 lat temu, zaraz po studiach, młody chłopak bez doświadczenia trafia do jednej z większych niemieckich firm z branży motoryzacyjnej. Obejmuje stanowisko specjalisty ds. przygotowania i organizacji produkcji. Pewnego pięknego dnia zgłasza się na dwudniowe szkolenie pod hasłem „Lean Manufacturing”. Nie wierzy w przypadki, a tu nagle szef się rozchorował i szukają kogoś kto zamiast niego weźmie udział w szkoleniu. To była dobra decyzja, choć przypadkowa. Bierze udział, szkolenie jest interesujące. Jeden ze szkolących poleca książkę Lean Thinking, niestety zarobki początkującego specjalisty nie pozwalają mu na jej nabycie. I znowu przypadek, albo łut szczęścia – pożycza tę książkę od jednego z menedżerów. Temat jest dla niego niezwykle fascynujący, pochłania lekturę w jedną noc. Gdy kolejnego dnia dzieli się wrażeniami z szefem, ten proponuje mu, aby zajął się Leanem w firmie. Przecież nikt w całej organizacji nie wie o Lean więcej niż on, tylko on przeczytał tę książkę. Wraca do domu nabuzowany energią. Nowe wyzwanie jest ciekawe, jednak on tak naprawdę nic o tym Lean nie wie. Zaczyna się zastanawiać, czy nie brakuje mu doświadczenia. Z drugiej strony to jednak okazja i niepowtarzalna szansa! Jedyne co posiada to młodzieńczy zapał i odrobina zdrowego rozsądku. Jak się potem okaże, zdrowy rozsądek to jest właśnie sedno Lean.

Szefostwo powierza mu tymczasowe stanowisko Lean menedżera. Początkowa ekscytacja powoli zamienia się w zwątpienie, pojawia się strach i niepewność, czy przypadkiem nie powinien się wycofać. Typowe uczucia dla drugiego etapu przejścia przez zmianę, kiedy zdajemy sobie sprawę, że oto nadchodzi nieuniknione. Gonitwa myśli w stylu „zrobiłem to sobie na własne życzenie”, czy „trzeba było siedzieć cicho, nie wychylać się i dalej przygotowywać dokumentację dla produkcji”. A zatem w swojej naiwności, nieprzygotowany i przerażony, wymyśla pewne rozwiązanie, które w jego odczuciu ma zwiększyć szansę powodzenia akcji pilotażowej. Prosi szefa o możliwość przydzielenia kolegi do pomocy. Dostaje 50% jego czasu. W ten sposób ma swój pierwszy w historii Lean team. Czyli półtora pracownika, licząc jego samego i 50% czasu kolegi, do tego pasja, chęci i młodzieńcza fantazja. Nadszedł czas, aby wypracować jakiś pomysł. W tym celu udają się po pracy na piwo. Kolega psuje podniosły nastrój prostym pytaniem, w jaki sposób będą to robić, ten cały „projekt Lean”. Odpowiada, że zwyczajnie, że pójdą na produkcję i będą obserwować ludzi przy pracy. Kolega nie daje za wygraną i dopytuje, czy to wystarczy. „Skąd mam niby wiedzieć?” – myśli, ale innych pomysłów nie mają.
Przez kilka miesięcy obserwują linię produkcyjną. Dziesięć godzin dziennie. W jeden tydzień uczą się o funkcjonowaniu organizacji więcej, niż przez cały poprzedni rok w pracy. A przecież pracowali sumiennie, zajmując się przygotowaniem i organizacją produkcji. Jednak przez ten rok nie byli na hali montażowej chyba ani razu. Nikomu nie przyszło nawet do głowy, że jest taka potrzeba. Nic nadzwyczajnego. Dziś, biorąc pod uwagę jego dwudziestoletnie doświadczenie, w ciemno może powiedzieć, że w większości firm menedżerowie nie zaglądają do pracowników i podejmują decyzje zza biurka, z dala od procesów, zarządzając produkcją z perspektywy czterech ścian swoich gabinetów. Niekoniecznie z wygody, zawsze przecież tak było, no bo niby i po co mieliby chodzić na tę halę, co by to zmieniło?
Spędzają więc miesiące między pracownikami liniowymi na produkcji. Przyglądają się pracy przy taśmie, pytają co ludziom przeszkadza. Nikt nie wyrywa się do współpracy, wręcz nie chcą, żeby zawracać im głowę. Zaczynają panikować, że wszystko weźmie w łeb. Wydawało im się logiczne, że pracownicy będą mieli jakieś pomysły. A tu nic. Traktują ich wręcz jak jakichś intruzów, wysłanych przez management na przeszpiegi. Wreszcie któraś z pań skarży się, że ma kombinerki zbyt daleko i wciąż musi po nie sięgać. Wykorzystują nadarzającą się okazję, ostentacyjnie przylepiają kombinerki taśmą klejącą w takim miejscu, że jest jej wygodniej. Kobieta dziwi się, że tak można, a inni zaczynają na nich patrzeć przychylniejszym okiem. Pracownicy powoli oswajają się z ich obecnością, a po nabraniu zaufania zaczynają się otwierać. Mówią o rzeczach, które im przeszkadzają w pracy. Zaczynają podnosić rękę, kiedy widzą problem, o co od samego początku bezskutecznie byli proszeni. Lean team stara się załatwiać wszystkie problemy na bieżąco, ale lider zmianowy poleca, aby skupiać się głównie na tych, które powodują zatrzymanie linii. Faktycznie, bardzo rozsądnie. Szefostwo dostrzega zmianę i udaje się wyprosić dla zespołu mechanika. Ludzie coraz aktywniej zgłaszają im marnotrawstwa, a oni zapewniają zasoby, narzędzia i sprzęt, by je wyeliminować. Kolejne problemy znikają. Tylko tyle. Codziennie robią z pracownikami podsumowania co udało się wyeliminować, poprawić. Po kilku miesiącach produktywność wzrasta o 20%. Dyrektor składa gratulacje, ilość dziennie zgłaszanych problemów sięga setki. Ludzie zachwalają atmosferę, są zaangażowani i uśmiechnięci. Management chwali się wynikami. Oprócz wydajności znacznie poprawia się jakość i terminowość dostaw. Dwu i pół osobowy Lean team ma powody do radości. Centrala przysyła ludzi, przyglądają się tej pilotażowej linii. Szef dywizji proponuje, aby rozszerzyć działalność i wprowadzić Lean w całej produkcji. Chwila zawahania i decyzja, że dla wszystkich to na hali się raczej nie da, że będą potrzebne szkolenia.
Lean to nie szkolenia
Nadchodzi więc moment, kiedy wszystkim z produkcji należy wytłumaczyć, nad czym tak właściwie pracuje ten Lean team. Jeśli powiedzą, że chodzi o samo obserwowanie i zadawanie pytań, to będzie zbyt proste. Ludzie będą się pytać, czy to wszystko i czy na tym polega ten cały Lean. Dochodzą do wniosku, że potrzeba jakichś narzędzi. Inspiracją w ich doborze było szkolenie, które wcześniej przeszli. Decydują się odejść od linii i rozszerzyć działania pilotażowe na cały zakład, opierając się na szkoleniach. W tym celu organizują salę szkoleniową i robią harmonogram szkoleń dla całej załogi. Co z ich linią pilotażową? Przyjmują, że ludzie sobie poradzą. Tak to wspólnie z nimi rozhuśtali, że nikt i nic tego nie zatrzyma. Takie podejście to fatalny błąd, ale nie są tego świadomi. Zostawiają ludzi bez impulsu w postaci kwestionowania status quo, obecności kogoś, np. lidera zespołu, kto obserwuje z boku i ciągle zadaje pytania. Jak się później okaże, to równia pochyła. Ciągłe doskonalenie działa tylko wtedy, gdy połączymy ze sobą dwa elementy: po pierwsze, pracownicy mają prawo podnosić rękę, kiedy widzą problem, a po drugie proces ten nigdy sam z siebie się nie zadzieje. Należy być w Gemba, zadawać pytania, okazać szacunek. Zgłaszanie sugestii umiera po pospolitym zrywie, jeśli brakuje ciągłych impulsów ze strony lidera. Kiedy więc orientują się, że ich Lean upada, ratują się uruchamiając system płacenia za pomysły. Niestety, nie daje to żadnego rezultatu, a wpływ na zaangażowanie pracowników w doskonalenie z tego żaden. Liczba rozwiązanych problemów na osobę spada niemal do zera.
Wracając do szkoleń, bo na tym się teraz koncentrują, przygotowują pospiesznie własne materiały szkoleniowe: trochę symboli, grafik w WordArt i gotowe. Całość nazywają „Lean Manufuckturing”, ale nikt nie zauważa literówki. Coraz więcej pracowników, liderów i menedżerów zgłasza chęć udziału w warsztatach, bo mają wtedy wolne od pracy. Pierwsze spostrzeżenia dotyczące szkolenia są niepokojące. Ludzie cały dzień słuchają o Lean, a potem jak gdyby nigdy nic wracają na linię produkcyjną i pracują tak, jak dotychczas, z tą różnicą, że posiadają dyplom ukończenia jednodniowego szkolenia, zresztą o „wdzięcznej” nazwie. Lean team nie chodzi już na halę, nie mają na to czasu. Zamiast tego całe dnie spędzają w sali szkoleniowej. Nie mówią już ludziom o konieczności podnoszenia ręki, ale rozwodzą się szeroko o narzędziach lean. Z upływem czasu ich materiały stają się coraz bardziej interaktywne. Pokazują filmy, zdjęcia, przykłady wdrożeń i pomysłów innych pracowników. Brakuje w tym jednak ducha rozwiązywania problemów w zespole, mającym wspólny cel, praktykującym na żywym organizmie, zajmującym się prawdziwymi, a nie wyimaginowanymi marnotrawstwami z pozycji czterech ścian sali szkoleniowej.

Szef Toyoty zapytany kiedyś, czym ich model zarządzania różni się od innych firm powiedział, że rozwiązują problemy tu i teraz, a inni zajmują się ich analizą. Wtedy nikt z Lean team tego przesłania nie rozumiał. A koszmarnym błędem było właśnie odejście od rozwiązywania problemów „tu i teraz”. Zadanie było jasne: szkolenia dla wszystkich plus raz w miesiącu spotkania, podczas których analizują najczęściej występujące problemy. Odeszli od rozwiązywania problemów „tu i teraz” na rzecz pseudoedukacji, statystyk, supernarzędzi, których nikt, łącznie z członkami Lean teamu do końca nie rozumiał.
Lean to nie szybsza praca
Spotykają się z 20% reprezentacją produkcji, by omówić najczęstsze błędy. Okazuje się, że na 250 błędów 160 dotyczy tego samego błędu – pomylenia brązowo-żółtego przewodu z żółto-brązowym przy montażu wiązek kablowych. Nasz Lean menedżer pyta o przyczynę. Cisza. Ponawia pytanie, wówczas jedna z kobiet oznajmia szeptem, że spaliła się żarówka na jej stanowisku. Żarówka, w związku z tym łatwo o pomyłkę kolorów, bo nie widzi ich zbyt dobrze. Wydawać by się mogło, że już nic bardziej kuriozalnego nie usłyszy, a jednak – żarówka przepaliła się… miesiąc temu. To typowa sytuacja zarządzania przez trzymanie kciuków, gdy liczymy że błędy nie wystąpią, a zarządzanie tematem miesiąc po, to już naprawdę jest „po ptokach”. Gdyby lider był na miejscu, gdyby pani była przez niego uprawomocniona i podniosła rękę od razu, kiedy zgasło światło, czyli w momencie wystąpienia problemu, sytuacja wyglądałaby zupełnie inaczej. Mechanik – jeden z członków Lean teamu – natychmiast deklaruje się założyć tam halogen. Zespół działa bez zbędnej zwłoki, już następnego dnia przenoszą się na linię produkcyjną, której nie widzieli od prawie pół roku, zajęci szkoleniami załogi. Obserwują panią pracującą przy halogenie, wokół niej kilka osób, które pomagają jej pracować dobrze. Mechanik zauważa, jak inny z pracowników bardzo mocno skupia się montując rzeczone kable. Leci do warsztatu, instaluje lupę na podstawce od starej lampy biurowej – pracownik może sobie powiększać te kable i montować je poprawnie. Po miesiącu liczba błędów spada o 90%. Niewiele wysiłku, koszt żaden – halogen plus stara lampka, a jakość pracy, satysfakcja i wdzięczność pracownika – bezcenne. Niestety, Lean team nie wraca do starego, dobrego zdrowego rozsądku, obserwacji tu i teraz. Patrząc na to z perspektywy czasu: zabrakło refleksji, sprawdzenia, jaki wpływ mają szkolenia na zachowania ludzi, ich zaangażowanie. A można było to zrobić, analizując chociażby liczbę rozwiązanych problemów.
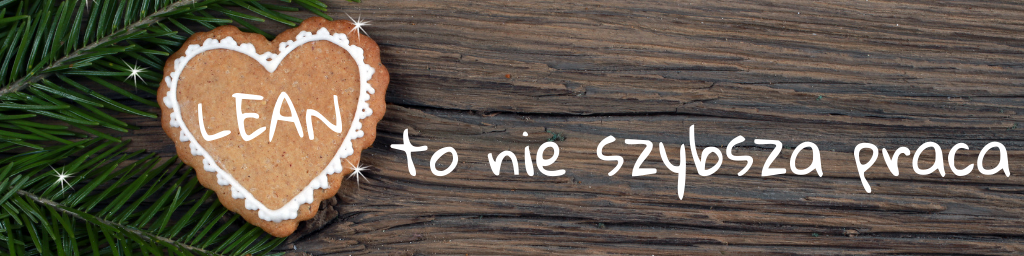
Jednakże, zwiększyli wydajność wszystkich linii dorównując do wyników linii pierwszej, tej pilotażowej. Różnica polegała na tym, że odbyło się to bez udziału pracowników, eliminacji marnotrawstwa i poprzez narzucenie, że skoro na jednej linii się dało, to inni tez muszą to osiągnąć. W efekcie ludzie pracowali ciężej, a nie mądrzej.
Lean to nie zestaw narzędzi
I to jest ten moment, kiedy naszemu Lean menedżerowi zaczyna uderzać do głowy woda sodowa. Przy jednoczesnym braku pokory i przekonaniu o swojej „zajefajności” decyduje się odejść z firmy. Szuka nowych wyzwań, obwiniając za niepowodzenie wszystkich innych, oprócz siebie samego. Oczywiste jest, że menedżerowie byli niecierpliwi, że chcieli zmiany za szybko, że podobał im się pomysł szkoleń. Ale do licha, kto odpowiadał za tę zmianę, kto spartolił szansę na zbudowanie trwałej kultury rozwiązywania problemów w swojej pierwszej firmie? Myśląc ciepło o udanych, wg niego, doświadczeniach z nieszczęsnym „Lean Manufucturing” zaczyna szkolić na całego w nowej firmie. Rozkręca się, a jego ego coraz mocniej daje o sobie znać. Chodzi na różne konferencje i opowiada, czym jest Lean. Jednakże w pewnym momencie zauważa, że większość tych dobrych historii dotyczy omawianej wcześniej linii pierwszej – tej pilotażowej. Kiedy to po raz pierwszy miał przyjemność „dotknąć” Lean i to z najlepszej perspektywy – prostoty i zdrowego rozsądku. Przychodzi moment refleksji. Załapuje się na treningi w Akademii Porche. Następnie uczy się bezpośrednio od Japończyków. Dojrzewa jako lider w GE, przez jakiś czas prezesuje w hucie szkła (zobacz też: historia o szklanych koniach). Wreszcie jest gotowy. Zakłada własna firmę, Leanpassion, a jego prezentacja zawiera już ponad 300 slajdów. Długo gromadził swoje materiały, ten skarb, który dumnie nazwał – już z poprawną pisownią – „Lean Manufacturing.ppt”. Tak, atrakcyjność wystąpień mierzy wówczas liczbą slajdów. Opiera biznes na szkoleniach otwartych. Przychodzą menedżerowie z banków, z produkcji i wielu innych branż. W ciągu dwudniowego szkolenia jest w stanie zapoznać ich z ponad pięćdziesiątką narzędzi Lean!
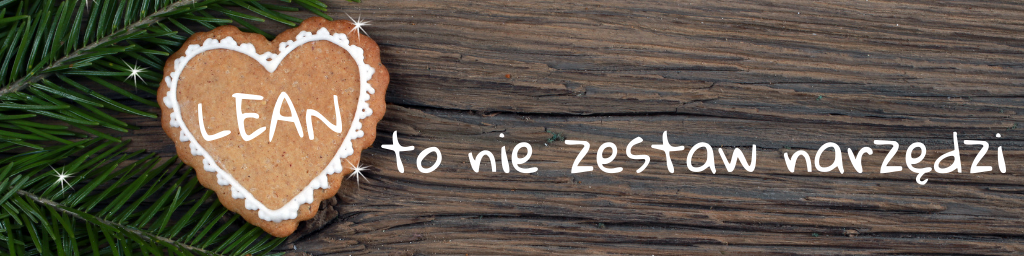
Jak menedżerowie oceniają te szkolenia? Dobrze, ale widać, że głowy im wręcz parują. W praktyce wracają do siebie, chowają materiały do szuflady biurka, wieszają przepiękne certyfikaty w ramkach na ścianie. A wiedza? Niestety nic z nią nie robią. Godzinami opowiada im, jak wspaniałe Japończycy powymyślali narzędzia, ale nie wyjaśnia, czym ten Lean tak naprawdę jest. Nie zapomniał, ale nie opowiada menedżerom o tym, jak zaczynał. Jak 10 godzin dziennie obserwował ludzi, zadając im pytania i rozwiązując wspólnie z nimi problemy. Gdzieś po drodze mu się ten Lean zapodział, a może przesłonił go setkami slajdów i zbyt dużą arogancją?
Dlaczego liderzy nie wierzą w siłę Lean?
Ta historia jest prawdziwa. Pochodzi z bestsellerowej książki STRATEGIA LEAN. Dlaczego w WIELKICH firmach ludzie nie mogą doczekać się PONIEDZIAŁKÓW. To klasyczny przykład pułapki, w którą wpadają ludzie rozpoczynający pracę z Lean. Na początku kierują się zdrowym rozsądkiem i działają jak prawdziwi mistrzowie. Są w Gemba, miejscu, gdzie dzieje się proces, gdzie pracują ludzie. Obserwują proces, zadają pytania i rozwiązują problemy. Nie zza biurka, nie w sali szkoleniowej. A potem przychodzi chwila pomroczności, że to przecież nie może być takie proste! Zaczyna się pseudo-uatrakcyjnianie tematu, kombinacja z narzędziami, indoktrynacja ludzi niezrozumiałymi pojęciami z japońskiego słownika Toyoty. Tak opakowane zagadnienie doskonale się sprzedaje, to fakt. Zresztą wielu ludzi jako skuteczne postrzega jedynie złożone wdrożenia. Są takie poważne, profesjonalne. Zdrowy rozsądek? Zbyt oczywiste, za proste! Właśnie dlatego tak wielu nie wierzy w siłę Lean – prostej identyfikacji i eliminacji marnotrawstwa. Ludzie pracują i podnoszą rękę, kiedy widzą marnotrawstwo. Lider dziękuje za problem i wspólnie szukają przyczyny jego wystąpienia oraz proponują pomysły na jego rozwiązanie.
Pozwól mi zrobić, a zrozumiem
Od momentu, gdy nasz Lean menedżer zaczął zadawać pytania ludziom przy taśmie i rozwiązywać problemy, historia zatoczyła koło. Dzisiaj jest dumny z tego, czym zajmują się ludzie w Leanpassion. Wrócił do korzeni. „Powiedz mi, a zapomnę. Pokaż, a zapamiętam. Pozwól mi zrobić, a zrozumiem.” To jest takie logiczne, takie zdroworozsądkowe.
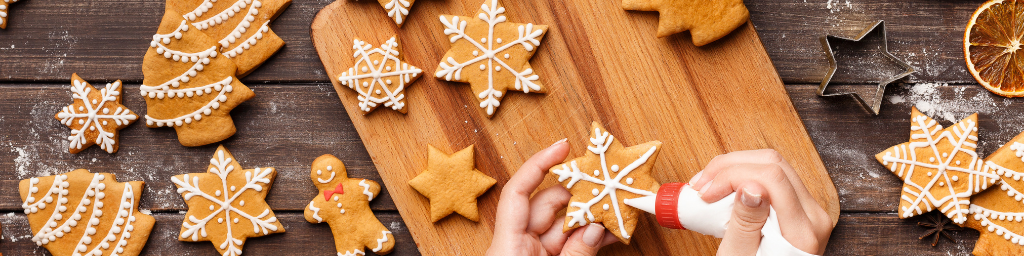
Wszelkie umiejętności tylko w 10% pochodzą ze szkoleń, w 20% z nieformalnych rozmów, a cała reszta – te 70% – z praktyki, z własnych doświadczeń. Jeśli pomyślisz o własnych doświadczeniach, to na ile te stwierdzenia mają sens? A teraz pomyśl, że Lean działa w jeszcze większym stopniu! I nie chodzi o to, aby Lean „wdrażać”, bo żeby być Lean trzeba stać się Lean. Trzeba ćwiczyć, praktykować, eksperymentować. Codziennie. Żeby się nauczyć, trzeba trenować. Z Lean jest jak z jazdą na nartach. Nie wystarczy przyglądać się, jak szusują inni. Najdroższy sprzęt nie jest wcale niezbędny. Jeśli nie wyjdziesz na stok, niczego się nie nauczysz. Jak się nie wywrócisz, to się nie nauczysz. Wtedy właśnie rozwijasz swoje umiejętności. Oczywiście pod warunkiem, że z każdej próby potrafisz wyciągnąć wnioski. Co było nie tak, co Cię to nauczyło. Nasz Lean menedżer zaliczył w swoim życiu wiele takich narciarskich muld, ucząc się dużo na własnych błędach. Nabierał doświadczenia. Ćwiczył i nieustannie ćwiczy zdając sobie sprawę, jak wiele jeszcze przed nim. Historia Radka Drzewieckiego zatoczyła koło. Wrócił do zdrowego rozsądku i pracy bezpośrednio przy procesie, ale obecnie w innej roli. To nie on zadaje pytania, lecz inspiruje innych, by je zadawali.
Nauka Lean to nie jazda windą, lecz chodzenie po schodach. Idąc po schodach, masz szansę przemyśleć swój kolejny krok, uczysz się, pokonując każdy stopień. Doceń szczególnie te, w których musisz cofnąć się o krok, przemyśleć, by móc wspinać się znowu. Jadąc windą na pewno nie zrozumiesz co działa, a co nie.
Radek Drzewiecki, STRATEGIA LEAN. Dlaczego w WIELKICH firmach ludzie nie mogą doczekać się PONIEDZIAŁKÓW
________________________________________________
Jeśli chcesz zadać nam dowolne pytanie na temat wyzwań biznesowych, przed którymi stoisz Ty lub Twoja firma, zapraszamy Cię na bezpłatną konsultację z ekspertem Leanpassion. To 15 min. w dogodnym dla obu stron terminie oraz najwyższy poziom udzielanych odpowiedzi.